TAMMOS
- TAMMOS
- 01.06.2016 - 30.05.2018
- Federal Ministry of Education and Research
- KMU-innovativ, Funding measure: Civil security, Funding area: Security research program (Sifo)
- 242,000 euros
- Prof. Dr. Wilhelm Nüßer
- Matthias Füller, Sebastian Scholz
- topocare GmbH, Rhineland-Palatinate State Fire Brigade Association, Koblenz City Fire Brigade, Bad Kreuznach THW office
Effective protection against flooding and more safety for the emergency services
TAMMOS project: Semi-autonomous machines and logistics for mobile flood protection
Floods and inundations pose a considerable threat to people, the environment and infrastructure in Germany. In many cases, however, the existing stationary flood protection systems are not sufficient to completely avert this danger. Mobile forms of flood protection are necessary, e.g. to cope with localized heavy rainfall or special water masses.
The BMBF-funded TAMMOS project is researching semi-autonomous systems that can protect dams from breaching in the event of flooding without endangering human life. The central task is to develop a mobile flood protection system for high-risk areas. These are areas where the risk to life and limb of the emergency services is high, but where greater damage could be averted by setting up protection. The project aims to set up the barrier and the necessary logistics using semi-autonomous machines so that even emergency services hardly have to intervene directly within a safety zone. This overall goal of mobile flood protection is divided into four sub-goals:
- Automated installation technology: The first step is to create a protective barrier by laying a sand-filled geotextile hose. The laying technology required for this has the advantage that it can be automated and large barriers can be built very quickly and flexibly with the help of the hoses. Based on this, a semi-autonomous machine demonstrator is to be developed that can operate in hazardous areas without the help of local operating personnel.
- Semi-autonomous machines: As this machine is able to build up protection significantly faster than previous shut-off methods, optimum feeding logistics are required to achieve this level of efficiency. Small semi-autonomous units are to be developed to take over this feeding. These machines pick up the sand outside the zone, find their way to the laying unit and feed it with the consumable material. Important secondary criteria for these semi-autonomous machine units are a low basic weight, maneuverability and off-road capability.
- Optimization through technical infrastructure: A suitable technical infrastructure (machine communication, process data) and control logic must be set up for the semi-autonomous processes. Both the swarm of feeding units and the laying machine must orient themselves in the process and constantly optimize themselves. A network could be set up via a centrally ascending drone. The creation of a hardware and software basis for the intelligent networking of the individual units is the basis for the semi-autonomous process.
- Software development: Practical suitability is an absolute requirement for the solution to the target problem described. To achieve this, the solution must be able to be integrated into the tried and tested processes of the emergency services that are in place today. In particular, the operations center must have constant information and intervention options. This is important not only because of the expert knowledge available there for the construction of flood protection barriers, but also to assess the further development of the flood situation. For optimal integration, the software to be developed as part of the project therefore allows rough planning prior to deployment, decision support during deployment and the derivation of input parameters for adjacent processes. These adjacent processes include the delivery processes for consumables (sand, textiles, etc.) to the defined high-risk area, the other flood protection measures taking place in the surrounding area and the overall integration into operational planning and management. The project must be connectable for this purpose.
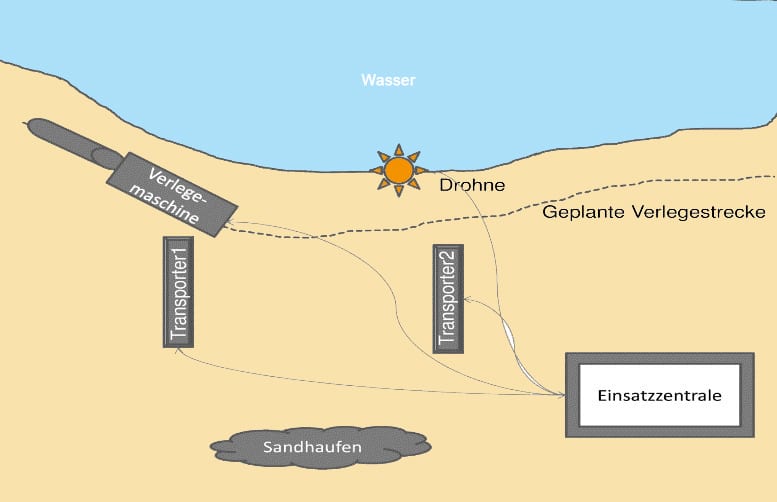
FHDW and topocare work together for greater safety in flood protection
As part of the project, the project partner topocare is developing mechanical engineering solutions for the semi-autonomous laying machine for sand hoses and the supplier systems. The FHDW is designing the necessary software systems to plan and control the individual systems and the overall logistics. As a result of the sub-project, demonstrators will be available for the control and coordination of the mobile units (laying machine and delivery machines), the control and integration of a drone into the process and the planning and decision-making support of the emergency services in the event of a disaster. While the control of the semi-autonomous laying and delivery machines is facilitated by the use of established robotics environments (ROS), logistics and planning tools must be completely redeveloped.
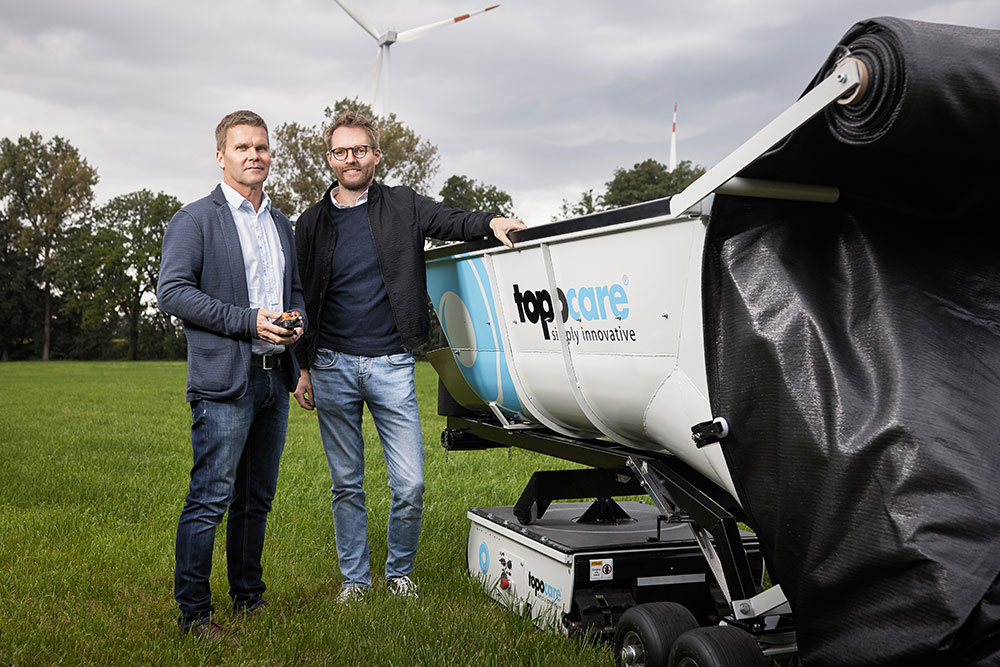
Among the top 20 most innovative projects at the German Future Prize
In 2020, the research project was put forward as a candidate for the German Future Prize. This makes it one of the 20 innovations selected for the award round.
Supported by
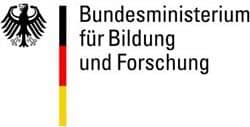